Среща на електрическите поколения: Технологичният път който BMW измина от Mega City Vehicle и i3 до Neue Klasse
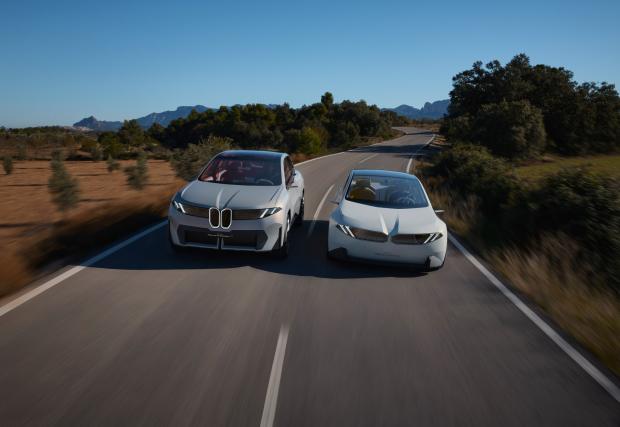
Времето отмина някак неусетно. Слушам презентацията на новите технологии за електрическо задвижване, обединени във философията на Neue Klasse, и мислено се пренасям във времето назад, когато през 2010 година BMW представи технологиите на Mega City Vehicle. Те от своя страна бяха плод на разработките, обединени под името Project i и се материализираха след това в първия сериен електрически модел на компанията i3. Новата концепция носи име, което трябва да символизира значимост, съпоставима с оригиналната „Нова класа“ от 1962 година и ролята изиграла за оцеляването, възхода и имиджа на BMW
От BMW дефинират новото електрическо задвижване като шесто поколение (Gen. 6), но задвижването на i3 всъщност е от трето поколение, защото е предшествано от Mini E и BMW Active E. Имах възможност тогава да шофирам първопроходеца Mini E, който на практика нямаше задна седалка и цялото задно пространство бе запълнено от възтежката батерия. Mini E с неговата склонност към загуба на сцепление на предния мост показа, че при електрическо задвижване задното предаване е по-подходящо и концепцията бе тествана именно при базираното на Серия 1 BMW Active E. Истинската революция обаче предстоеше да се случи, защото i3 бе автомобил изначално проектиран като електрически и стана носител на толкова авангарда техника, че и до ден днешен мнозина съжаляват за прекратяването на производството му.
Технологичните презентации на „Новата класа“ се случват в завода на BMW в Ландсхут, който още тогава се превърна в развоен и производствен център в областта на карбоновите конструкции за едросерийно производство, формиращи поставената върху алуминиева рама и изработена от усилени с въглеродни влакна полимери каросерия. В трудното и предизвикателно начинание за създаване на карбонов автомобил с приемлива себестойност, и в което BMW стана пионер имаше логика – инженерите от баварската компания се стремяха да намалят колкото се може повече теглото на самия автомобил, за да компенсират теглото на батерията и да формират дънна конструкция, в която на разположат корпуса на батерията с изработени от Samsung литиево-йонни клетки.
Born Electric 2.0
Тук в главата ми изниква още една история, която хората от BMW с достатъчно стаж в компанията с респект си спомнят…
Днес един от двата основни доставчика на литиево-йонни клетки е компанията CATL, но когато BMW търси доставчик на клетки за i3, просто не съществуват компании с опит в създаването на големи литиево-йонни клетки, както и обединяването им в акумулаторни пакети. Един от главните „виновници“ за стремителния ръст на днешния гигант CATL и известността на неговия шеф Роберт Зенг е Херберт Дийс, който през 2010 година все още е мениджър покупки за BMW и отговорен за връзките с доставчиците. В рамките на Project i и разработването на i3 BMW се нуждае именно от безалтернативните литиево-йонните клетки за батериите. Дийс (който по-късно стана главен изпълнителен директор на Volkswagen), се заема с нелеката международна мисия да убеди компании, произвеждащи батерии за мобилни телефони, да се ориентират към производството на клетки и батерии за електрически автомобили. Опитът му с германската Bosch е неуспешен, по скоро заради факта че Bosch се разделя със Samsung SDI и се оттегля от предприятието SB Limotive, което е трябвало да стане доставчик на i3 (впоследствие доставчик за i3 ще стане именно Samsung SDI). Но Дийс се среща и със Зенг, който по това време все още управлява фирмата ATL, дъщерно дружество на японската компания за електроника TDK. Наскоро Дийс разказа, че Зенг е погледнал на предложението с голяма доза пренебрежение и по това време е смятал че е невъзможно да създаде толкова голяма батерия на базата на съществуващите технологии.
И все пак Зенг не остава равнодушен към предложението. През 2011 г. той ръководи група китайски инвеститори, които придобиват 85% дял в бизнеса с батерии за електромобили на TDK. Компанията е наречена CATL, и именно BMW става първият ключов клиент. „Дийс отвори за нашата компания бизнеса с автомобилни батерии“, каза преди няколко години Зенг и допълни „Благодарен съм му за това.“ Четири години по-късно друга група инвеститори купува и останалите 15 процента от CATL.
На практика когато по-късно BMW решава да предложи на CATL да стане един от доставчиците на литиево-йонни клетки за автомобилите на компанията, Зенг внимателно прочита 800-те страници изисквания точка по точка. Вниманието на предприемача към детайлите е ключово.
Повече за тази история можете да прочетете в поредицата ни са историята на CATL, който както казахме, заедно с Eve Energy е един от доставчиците на литиево-йонни клетки за BMW.
Нов тип архитектура на батериите
Именно те са в основата на изцяло новия начин на изграждане на батерията на електрическото задвижване на Gen.6. Архитектурата на батерията на моделите Neue Klasse, първите от които ще започнат да напускат завод в Дебрецен още това лято е коренно различен от сегашната, използвана при моделите, базирани на модифицирани версии на платформата CLAR.
Цялото електрическо задвижване, респективно всички електрически машини използват по-ефективната 800-волтова архитектура. Призматичните (с форма на паралелепипед) литиево-йонни клетки за заменени с цилиндрични, които вече не се поставят в модули, а директно в корпуса на акумулаторната батерия (“cell-to-pack”) и сами по себе имат с 20 процента по-висока енергийна плътност от досегашните. Това спестява тегло и обем, а благодарение на новата архитектура зареждането може да става до 30 процента по-бързо и да осигурява с 30 процента увеличаване на пробега. Допълнително тегло се спестява от новия начин на изграждане на подовата конструкция на автомобила – батерията не се прикрепва към цялостно дъно на каросерията на автомобила, а се превръща в структурен компонент при което дъното на каросерията е изцяло отворено (“pack-to-open-body”). Вътрешната архитектура на клетката все още е тайна и засега не е ясно дали BMW ще използва така наречения immersion cooled battery pack, при който клетките се охлаждат и затоплят директно от водна риза, или досегашния вариант със серпантини и топлопроводим свързващ материал. От BMW твърдят, че прецизният топлинен мениджмънт на клетките е бил ключов параметър при проектирането на батериите.
BMW има два собствени отдела за развойна дейност в областта на батериите и литиево-йонните клетки, както и малък пилотен завод за клетки, но от компанията не смятат сами да ги произвеждат. За подобно нещо BMW няма необходимите производствени обеми, а целта е натрупване на познание в областта на електрохимията с цел по-добър контрол на батерията. Като част от този процес компанията сама е разработила и произвежда силовата електроника в специално обособена част на завода в Ландсхут с изключително високо ниво на чистота на въздуха. Самите батерии ще се произвеждат на принципа „локални за локални“, съответно в Ирлбах-Щраскирхен (Долна Бавария), Дебрецен (Унгария), Шенянг (Китай), Сан Луис Потоси (Мексико) и Уудръх, край Спартанбърг. За да покрие нуждите от литиево-йонни клетки за всеки един от заводите в Европа, Китай и САЩ, BMW Group има договорни отношения за пет завода за клетки с различни партньори.
Заводът в Ландсхут продължава да бъде централно звено и ключов компонент за моделите с електрическо задвижване. Силовата електроника, която от BMW наричат Energy Master ще се произвежда именно в този завод и след това ще заминава за всички останали локации за производство на батерии. Производственият процес не ползва поточна организация, а прецизно контролирана смесена последователност с 400 робота. В рамката на същата конгломерация от производствени предприятия са и леярните за алуминиеви блокове, цилиндрови глави и корпуси на електрическите мотори, които след това се транспортират в завода Щайер в Австрия, където се произвеждат електромоторите и се окомплектова цялото задвижване. Леярните за алуминиеви компоненти изискват изключително голямо количество енергия, но BMW притежава огромен експертен опит в създаването на нови производствени процеси, като използването на сърцевини, включващи нетоксични неорганични материали.
Електрическото задвижване
BMW може и да е пословичен със проектирането и производството на високотехнологични бензинови и дизелови двигатели, но с i3 компанията навлезе в изцяло нова територия. Това не и попречи още тогава да създаде високотехнологичен хибриден електрически мотор. И в случая „хибриден“ означава нещо съвсем различно от общото възприятие за този термин в автомобилостроенето. Става дума за синхронен електрически мотор с постоянни магнити, който в определени режими работи като „релуктантен“. В конвенционален режим „пълзящото“ магнитно поле на статора си взаимодейства с това на ротора. Проблемът е че в режими на високи обороти загубите стават значителни. Тогава хибридният мотор преминава към различен начин на взаимодействие между статора и ротора. „Релуктантността“ или магнитното съпротивление е термин обратен на магнитната проводимост по подобие на електрическото съпротивление и електрическата проводимост на материалите. При двигателите от този тип се използва явлението при което магнитният поток се стреми да премине през частта от материала с най-малко магнитно съпротивление. Като следствие от това той измества физически материала през който протича, за да премине през частта с най-ниско съпротивление. Този ефект се използва в електромотора за създаване на въртеливо движение – за целта в ротора се редуват материали с различно магнитно съпротивление, така наречените твърди (под формата на феритни неодимови дискове) и меки (стоманени дискове). В стремежа си да премине през материала с по-ниско съпротивление магнитният поток от статора завърта ротора докато не се позиционира така че това да се случва с минимално съпротивление. С управление на тока полето постоянно завърта ротора в удобно положение.
При електрическите автомобили от следващите BMW i3 модели, базирани на модифицирани версии на платформата CLAR (като iX, i4 и i5), компанията премина към синхронни мотори с електрическо възбуждане – така наречените EESM, при които магнитното поле в ротора се създава от постоянен електрически ток. Тяхната ефективност е близка до тази на синхронните с постоянни магнити, но се избягва използването на редкоземни материали, освен това може да се контролира и променя прецизно взаимодействието между полетата. За Gen. 6 моторите на задния мост запазват този тип работа, но са модифицирани за работа на 800 волта и са претърпели някои конструктивни промени. Съществената разлика е преминаването към задвижване с асинхронен мотор на предния мост, в който създаването на магнитно поле в ротора става чрез магнитна индукция в ротора. Пресичането на намотките на ротора от магнитните силови линии от полето създадено от статора води до протичане на ток в ротора по подобие на взаимодействията при трансформатора. Създаденото в резултат от това магнитно поле си взаимодейства с „въртящото“ се в статора и това води до механично увличане на ротора и последващо въртене. При този тип електромотори обаче роторът винаги изостава спрямо полето, защото ако няма относително движение между полето и ротора, няма да си индуцира магнитно поле в ротора. Така нивото на максималните обороти се определя от честотата на захранващия ток и натоварването. Въпреки по-ниската си ефективност асинхронните мотори са добро решение при непостоянно използване, защото не използват скъпи магнитни материали или сложни намотки в ротора и имат възможно най-ниската себестойност.
За задвижването се използва основно електрическия мотор на задния мотор, който работи при по-високо натоварване и при по-ефективни режими. Предният мотор се активира основно при ускоряване и когато автомобилът се нуждае от по-добро сцепление. Архитектурата на „Новата класа“ позволява използване на един, два, три и дори четири мотора, както и модулна концепция на електрическите машини в зависимост от нуждите.
Текст: Георги Колев