Анатомията на един автомобил: Citroen C3 – от проектирането до производството
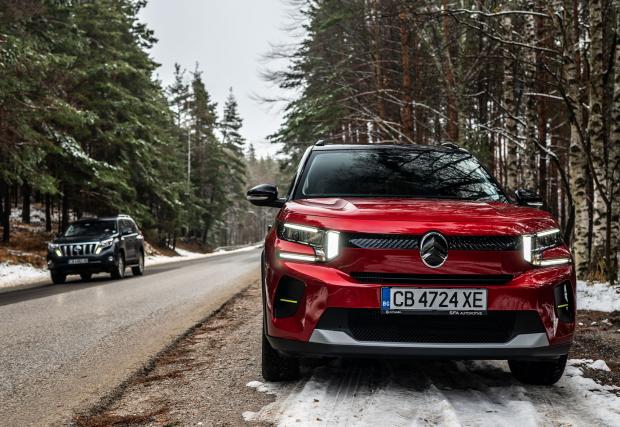
Как се създава високотехнологичен европейски автомобил на конкурентна цена
Възможно ли е да се произвежда достъпен автомобил с високо съотношение между качества и цена в Европа, на фона на силната конкуренция от китайската автомобилна промишленост? Отговорът е – изключително трудно, като имат предвид фактори като достъпа на Китай до енергийни ресурси на много по-ниски от европейските цени, по-ниските равнища на заплащане на труд и огромни икономии от производствените обеми, благодарение на големия китайския пазар. Към всичко това се добавят гарантирани доставки на суровини за акумулаторни батерии на умерени цени на базата на собствени и подкрепяни от държавата добиви или дългосрочни договори.
Съдейки по това което направи Stellantis с модела на Citroen C3, отговорът е – все пак да. При това, както във формат с бензиново задвижване, така и с хибридно и с чисто електрическо. Разковничето е в интелигентно конструиране на автомобилите и изграждане на цялостната верига на доставки, както и използването на високотехнологични производствени методи. Целта е да се предложи на клиентите автомобил, който предлага цялостно възприятие за качество, комфорт и безопасно поведение на пътя и за целта е впрегнат потенциала на хиляди инженери.
В този материал ще ви обясним в детайли как технологично се постига това – от начина на конструиране на платформата, през използваните авангардни решения за двигателя с вътрешно горене, хибридната компановка, електрическото захранване и задвижване. Специфични данни, характеристики и конкретно оборудване на C3 можете да откриете на самия сайт на Citroen в България Новият Citroën C3 - Емблематичният градски автомобил | Citroën
Високотехнологичен бензинов двигател
Въпреки очакваното, в новия C3 дори в базовата версия няма да срещнете някакъв архаичен двигател с атмосферно пълнене. Напротив, малкият автомобил, който се е превърнал в ярко отличим със своите форми SUV модел в малък формат, се задвижва от новия бензинов агрегат EB2 Turbo Gen3 с турбопълнене. Още първото поколение на 1,2 литровият EB Pure Tech трицилиндров двигател с принудително пълнене беше високотехнологична машина, която функционираше по цикъл на Аткинсън с ранно отваряне на изпускателните клапани, и разполагаше с изпускателни тръби с водна риза и интегриран турбокомпресор, директно впръскване с максимално налягане от 200 бара, както и степен на сгъстяване от 10,5:1. Конструкторите на тогавашното обединение PSA избраха конфигурация с работен обем от 1,2 литра като добър компромис за диапазона на мощност от 101 к.с. до 155 к.с., с бърза реакция на турбокомпресора и ранно разгъване на въртящия момент при сравнително дълъг ход на буталото (диаметър х ход 75 х 90,5 мм) и намалено ниво на триене. Той предлагаше отлични характеристики по отношение на разгъването на въртящия момент и ефективността и стана основа на множество модели от богатата палитра, първоначално на PSA, а по-късно и на концерна Stellantis.
Трицилиндровият двигател е оптимално решение по отношение на турбопълненето, заради времевата отдалеченост на работните цикли и почти пълната липса на негативно взаимно влияние на пулсациите при отваряне на клапаните. Турбината на Pure Tech достигаше максимални оборотни режими от 270 000 об./мин, а максималният въртящ момент от 240 Нм при най-мощната версия бе наличен още при 1750 об./мин.
Новият двигател с кодово име EB2 Turbo Gen3 вече е трето поколение на тази машина и заимства много от прийомите на предшественика си, но е усъвършенстван в дълбочина, като според създателите си вече използва работен цикъл на Милър. Той е една от предпоставките за още-по-ниското ниво на разход на гориво и емисии, в момента вече покрива нивото Euro 6e и има потенциала за постигане на Euro 7.
Част от съществените разлики при новия двигател са увеличеното до 350 бара налягане на впръскване, турбокомпресорът с променлива геометрия (VNT) и увеличена до 11,5:1 степен на сгъстяване. Изцяло променена е настройката на отварянето на всмукателните клапани, респективно работата на системата за променливо газоразпределение. И при този агрегат е реализиран цикъл на удължена работна фаза на двигателя с цел извличане на повече енергия от газовете, но тя е постигната по различен начин. В предишния двигател се реализира „цикъл на Аткинсън“ с късно затваряне на изпускателните клапани и връщане на част от всмукания въздух обратно, извън цилиндъра и във всмукателните колектори – с продължителност (фаза) на отваряне на всмукателните клапани от 220 градуса завъртане на коляновия вал. При новия агрегат, се използва вариант на по-ранно затваряне на всмукателните клапани с времетраене от 160 градуса (по-малко от хода на буталото). В двата случая се говори, съответно за цикъл с по-късно затваряне (LIVC, Late Intake Valve Closure) и по-ранно затваряне (EIVC, Early Intake Valve Closure). Някои компании, като Volkswagen дефинират и двата варианта като Милър цикъл, но конструкторите на EB2 предпочитат да ги определят като „цикъл на Аткинсън“ и „цикъл на Милър“. На практика, в това няма особено значение, защото и в двата случая се намалява количеството на всмукания и сгъстен въздух, респективно вероятността за детонации на гориво-въздушната смес, като реално се ограничава всмукателния такт, при запазване на продължителен работен такт. С това се повишава ефективността на горивния процес, извлича се повече енергия от газовете и се намалява температурата на отработилите газове, както и необходимостта от обогатяване на сместа в по-широк диапазон. Разликата спрямо използвания досега цикъл на Аткинсън е, че вече не съществува обратен поток, който влошава движението на въздуха във всмукателния колектор, а фазите на впръскване може да са по-малко сложни, тъй като липсва опасността от връщане на гориво-въздушна смес във всмукателните колектори. Допълнителен бонус са намалените помпени загуби, защото пълненето може да става с по-широко отворена дроселова клапа – тоест налице е още една предпоставка за подобряване на ефективността.
Въпреки своите предимства тази реализация на цикъла на Милър има и недостатъци в определени работни фази, като намаляване на въртящия момент при малки и големи натоварвания, когато са необходим респективно въртящ момент и мощност. При този цикъл се ограничава количеството нагнетен въздух, ефективната степен на сгъстяване, а намаленото налягане в края на работния цикъл, в резултат от по-голямото количество усвоена енергия, води до намаляване на налягането на газовете и ефективността на работата на турбината. За да се компенсира това, конструкторите прибягват до определени трикове. Те компенсират загубеното количеството на вкарания в цилиндрите въздух чрез увеличаване на налягането на пълнене в широк диапазон от обороти. За целта е взето решение за използване на турбокомпресор с променлива геометрия (VNT) – изключително рядко за едросериен бензинов автомобил и още по-малко в ниския ценови диапазон. Подобно решение използва например високотехнологичния 9A2 в моделите Turbo на Porsche 911.
VNT турбокомпресорите са широко използвани при дизеловите двигатели, но заради по-високата температура на газовете при бензиновите изискват съобразяване на материалите, използвани за насочващите лопатки. Последните променят и насочват потока на газовете в зависимост от количеството газове (обороти и натоварване) към турбината. Като част от мерките за компенсиране на гореспоменатите недостатъци геометричната степен на сгъстяване при ED2 Turbo Gen3 е увеличена от 10,5:1 на 11,5:1, което също е предпоставка за подобряване на ефективността и намаляване на разхода на агрегата. Изцяло нова е системата за контрол на променливото газоразпределение с управление със соленоидни клапани. Предишният ангренажен ремък е заменен с така наречената „тиха верига“, която има по-дълъг срок на работа.
Подобно на решенията при високотехнологичните мотори системата за впръскване на Bosch е с централно разположени електромагнитни инжектори и налягане от 350 бара, благодарение на което се осигурява по-равномерно разпределение на частиците гориво във въздуха. Налягането се контролира в зависимост от вида на работа, за да не се „обливат“ стените и буталото и за да се намали образуването на твърди частици. Принос за това има и въпросното по-високо налягане, осигуряващо създаване на частици с по-малък размер и по-висока кинетична енергия, респективно по-добро изпарение. Благодарение на гореописаното двигателят може да адаптира работата си спрямо октановото число на бензина в диапазона 91-98.
Към всичко това се добавят вакуумно лят алуминиев блок с допълнителна топлинна обработка с интегрирани алуминиеви втулки с допълнително покритие на стените, алуминиева глава, четири клапана на цилиндър, стоманен колянов вал и единичен балансиращ вал и филтър за твърди частици.
Благодарение на всичко гореописано двигателят, който за C3 се предлага с мощност от 100 к.с. и въртящ момент от 205 Нм осигурява изключително балансирано и динамично поведение на автомобила с тегло от 1151 кг килограма, нисък разход на гориво, висока надеждност и спокойствие, че може да се движи и в зони с ограничени нива на емисии.
Ефективно 48-волтово хибридно задвижване
Във версията със задвижване с бензинов двигател се използва шестстепенна ръчна трансмисия, но C3 ще предлага на клиентите си възможност за хибридно задвижване. В името на оптимизацията на разходите конфигурацията включва 48-волтова система, но за разлика от повечето технологични решения от този тип, тя не е с ремъчен стартер генератор (P0), а с интегриран в предната част на трансмисията електрически мотор (P2). Тази връзка създава най-оптимални условия за работа без загуби и максимално ниво на усвояване на рекуперативната енергия, благодарение на наличието на съединител между двигателя и скоростната кутия. Така, при намаляване на скоростта на автомобила, двигателят с вътрешно горене не създава спирачно усилие и последното се поема от електрическата машина, която генерира ток. По същата конструктивна причина системата позволява и директно електрическо задвижване, без необходимото преодоляване на триенето в двигателя с вътрешно горене, както при свързаните с ремък 48-волтови системи. Citroen C3 и C3 Aircross от B и B-SUV са най-малките модели, чието достояние е тази хибридна трансмисия – тя е част от задвижването и на по-големите моделни линии на C4 и C5 от C, C-SUV и D-сегмента.
Архитектурата с ниско напрежение е избрана като най-добро съчетание от ефективност и себестойност, а 48-волтовият електрически мотор е интегриран в трансмисията с два съединителя eDCT. Той е свързан с първичния и вал със зъбна предавка с предавателно отношение от 3,04:1 (повече за тази специфична и сложна сама по себе си скоростна кутия ще ви разкажем в поредицата за еволюцията на трансмисиите в секцията Анатомията на автомобила). С това допълнително се увеличава добавеният към този на ДВГ въртящ момент и пълноценно се използва големият оборотен диапазон на 15,6-киловата електрическа машина на Vitesco. Интересно по своята същност е решението на мястото на генератора да се постави втора 48-волтова електрическа машина, чиято задача е да рестарира адаптирания (с нискофрикционно покритие на лагерите) за множество стартове двигател след циклите на изключване. Голямата електрическа машина в трансмисията има функцията на тягов мотор и генератор, но стартира двигателя при студен старт. Ремъчният стартер, произвеждан от Valeo не играе ролята на генератор, при студен старт прилага само лек въртящ момент, за да осигури опън на ремъка за задвижване на периферните агрегати като климатичен компресор, а при изключване на двигателя създава лек негативен въртящ момент в името на плавното спиране с по-малко вибрации. Отделно, електрическата система включва и 12-волтов акумулатор, както и преобразувател от постоянно в постоянно напрежение (12V-48V) за захранване на 12-волтовата бордова електрическа система. В случай, че автомобилът е престоял дълго време и 48-волтовата батерия е с ниско ниво на заряд, инверторът трансформира тока с напрежение от 12 волта в 48 волта, за да захрани стартера. С цел по-бързо отопление на купето се използва 48-волтова термисторна матрица (PTC полупроводници, които се нагряват при протичане на ток и увеличават съпротивлението си при повишаване на температурата), а компресорът на климатичната система се задвижва също от ремък.
Според Citroen, при градско шофиране на C3, до 50 процента от движението може да бъде осъществено в чисто електрически режим, до 1 км може да се измине на електричество, освен това системата постоянно подпомага двигателя, осигурявайки възможност за по-плавно движение и възможност за използване на режими на по-висока предавка, респективно работа на двигателя в по-ефективни режими. Дори и при спиране от скорост от 150 км/ч на магистрала електрическата машина може да рекуперира енергия.
Гореописаният двигател ЕD2 е претърпял някои модификации за целите на хибридното задвижване с допълнителни монтажни елементи, 48-волтов стартер на мястото на генератора и пълно отпадане на 12-волтовия стартер. Добавени са две електрически водни помпи за охлаждане на електрическото задвижване.
Mild хибридното задвижване използва шестстепенна електрифицирана скоростна кутия с два съединителя, конструирана от съвместното предприятие на Stellantis и Punch Powertrain e-Transmissions се произвежда в предприятието на Stellantis Group в Метц. Както въпросните съединители, така и свързващият електромотора с ДВГ съединител са „мокър тип“ в маслена баня, с допълнителни маслени и охладителни кръгове за цялата трансмисия.
Тяговият електромотор от своя страна е високооборотен 6-фазен агрегат, с постоянни магнити и медни намотки на статора. Грижа за цялостното управление на системата има 48-волтов DC-DC инвертор с 12 силови транзистора (по 2 на фаза) на Valeo.
Цялото това технологично решение е по-скоро рядкост в малките класове като този на C3 и C3 Aircross. Благодарение на мощния електромотор ефективността му е почти равностойна на тази на по-сложни паралелно-последователни (Toyota) или последователни хибридни системи (Honda), при по-ниска цена, а резултатът от всичко това е още по-нисък разход на гориво. Добавеният въртящ момент, помага за по-плавното задвижване и честото движение на електричество.
По подобие на повечето хибридни системи батерията на тази система използва сравнително тесен диапазон от капацитета – 50 процента в диапазона 25-75 процента ниво на заряд. Това се прави с цел удължаване на живота и поради големия брой зареждания и разреждания в цикъла на работа. Батериите за Plug-in хибриди например използват около 75% от брутния капацитет на батерията, а тези за електрически автомобили – около и над 90%. Във версията за Smart Car Platform литиево-йонната батерия с брутен капацитет от 0,897 кВтч има нетен капацитет от 0,432 кВтч, разположена е под предната лява седалка, има нискотемпературен кръг за охлаждане под нея и трябва да осигури функционалност на задвижването в рамките на целия живот на автомобила.
Дизайн на SUV, мултиенергийна платформа и адаптивна ходова част
Както C3, така и е-C3 и по-големите C3 Aircross са базирани на новата модулна платформена система Smart Car Platform, която е модификация на досегашната CMP и позволява реализацията на различни дължини. Тя включва висок дял на високоякостни стомани в ключовите за здравината и безопасността зони на пътническата клетка, областта в основата на педалите, A- B- колоните, като за част от тях е използван процес на топлинно формоване. В определени части на деформируемите зони поемащи кинетичната енергия при удар са използвани и компоненти от екструдирани алуминиеви сплави. Свързването на компонентите е базирана на комбинация от точково заваряване, дъгово заваряване, закрепване с болтове и структурни лепила.
Кликнете на изображението и се запознайте с конкретни ценови предложения за модела
Голямото предимство на тази платформена система е възможността за производство на една и съща поточна линия на варианти както със задвижване само с бензинов мотор, така и на хибридно и чисто електрическо задвижване. Технологията позволява лесната промяна на определени носещи компоненти в дънната конструкция и адаптацията на монтажните точки за ДВГ и електрическо задвижване и управляващата електроника в предната част. Конфигурацията на подовата конструкция на версията с електрическо задвижване е такава че отпада тунелът за ауспуховите тръби, а към дъното е прикрепена тежащата около 350 кг тягова батерия (във версията с 44 кВтч) батерия. Нейният солиден носещ алуминиев корпус се превръща в част от структурата на автомобила, която осигурява необходимата при увеличеното тегло здравина и по-нисък център на тежестта. Поради този факт дъното, респективно подът на електрическата версия е леко повдигнат. Именно на увеличеното тегло се дължи интересният факт че електрическата версия е с дискови задни спирачки, а бензиновата с барабанни. Тъй като автомобилът се задвижва от предния мост и той поема рекуперативните функции, е взето решение за използване на задни спирачки с по-голям капацитет при електрическия модел.
Както и по-големите модели семейството на C3 използва в голяма степен електронни и софтуерни архитектури, също определяни като платформи. Те осигуряват управлението не само на задвижванията, но и на цялостния комплекс от сложни системи за активна безопасност и включват микропроцесорни системи с радарни сензори и камери, свързаност и навигация. На тази база системите притежават възможността за актуализации по въздуха. Ясно видимият и ергономичен дисплей на височината на погледа в C3 е само малък израз на електронните системи, които стоят зад него.
Поведение на пътя: амортисьори с прогресивни хидравлични възглавници
Още едно технологично решение, използвано и заимствано от големите модели е ходовата част с така наречените прогресивни хидравлични възглавници (progressive hydraulic cushions). Хидропневматично окачване на Citroen е знакова част от автомобилната история с представянето му в DS, а в ходовата част на C3 и C3 Aircross е въведена система, която по различен начин успява да съчетае комфорта при преминаване през неравности със стабилността при завои. Историята на амортисьорите с хидравлични демпфери може да се проследи назад до модела ZX Grand Raid, предназначен за тежки състезания, като рали Дакар и по-късните рали автомобили от долните класове. За първи път такива се въвеждат в сериен модел на Citroen при C4 Cactus през 2018 г. и по-късно при C5 Aircross.
За какво става дума – на практика към основният класически хидравличен амортисьор е добавена система от допълнителни компоненти в двата му края. За разлика от системите с еластични ограничители, тази не връща енергията (течностите са несвиваеми), а просто променя характеристиките на амортисьора в крайните фази на сгъване и разширение. Все пак в общата конструкция са добавени и полимерни елементи, но те служат само за ограничаване на силата при най-крайни фази на движение, за да не се повредят метални части при резки натоварвания на окачването.
Просто казано, настройката на амортисьора в негова условна средна част е изключително комфортна. Когато обаче амортисьорът се свие до определена степен, като например на външните колела, при взимане на завой, той започва прогресивно да се втвърдява като маслото под допълнително, съосно с основното, бутало в обема на долната цилиндрична хидравличната възглавница преминава през калибрирани отвори, чийто диаметър и брой се намалява. По този начин се намалява дебитът на преминаващото масло в преливната камера, оставащата течност създава по-голямо хидравлично съпротивление и амортисьорът става по-стегнат. При фази на удължаване на амортисьора (например на външните колела при завой) маслото в обема на горната хидравлична възглавница преминава през прорез в разделен пръстен. Тъй като формата на тръбата в която се движи буталото във възглавницата е конична, разделеният пръстен, притиснат от буталото на хидравличната възглавница се свива и стяга по неговия ход, в резултат от което масленият поток се намалява и амортисьорът се втърдява, но този път във фаза на разширение. По този начин в средната си част амортисьорът остава „мек“, осигурява невероятно за автомобил от този клас комфортно поведение в субективното възприятие за магическото килимче Magic Carpet, а при свиване и при разширяване прогресивно се стяга, като начинът по който става това в двата случая е различен.
Електрическо задвижване с уникални възможности
Както споменахме, като модификация на платформата CMP Smart Car Platform предлага и конфигурация за електрическо задвижване. То включва два варианта на захранване с акумулаторни батерии с литиево-желязо фосфатни (LFP) клетки и капацитет от съответно 44 и 30 кВтч. Въпреки, че има малко по-ниска енергийна плътност от никел-манган кобалтовите клетки (NMC), този тип електрохимия става все по-популярна напоследък, заради отличното съчетание на качества – по-добра защита от възпламеняване, по-ниска себестойност и пълна липса на скъпи катодни материали. LFP клетките имат малко по-ниско работно напрежение (прибл. 3,0 V при 10% заряд до 3,4-3,6 V при 100% заряд), но позволяват безпроблемно зареждане и до 100 процента, имат изключителна надеждност, висока температурна и химическа стабилност и ниско ниво на деградация.
Производител на клетките е китайската фирма Svolt, която е един от лидерите в тази област, разполага с развоен център с 2500 служителя, от които над 1000 с различни научни степени, а нейната технология с призматични клетки наречени Short Blade е сред най-добрите в тази област. Заводите на Svolt в Янченг, Шангао и Ченгду използват технологията Fly Stacking, която гарантира бързо и ефективно производство с високо ниво на качество. Конструкцията на катода (най-сложната и скъпа част от литиево-йонната клетка) включваща блок от железни сплави и фосфорна киселина се произвежда с максимално ниво на чистота. Батерията на C3 с капацитет от 44 кВт включва два модула с по 50 последователно свързани клетки, всяка с брутен капацитет от 143,5 Ач и нетен от 140,2 Ач (осигуряващи най-доброто съчетание от себестойност и енергийна плътност от 180 Втч/кг). Двата модула са свързани също последователно – оттам и формулата на свързване 1P100S (100 последователно свързани клетки). Всяка клетка е с капацитет от около 0,45 кВтч, а работното напрежение в зависимост от заряда е между 300 и 360 волта. Пример за качествата на клетките е фактът, че акумулаторният пакет на C3 използва почти целия си брутен енергиен капацитет от 45 кВтч и е с C-фактор над 2,2 – при номинален капацитет от 44 кВтч тя може да бъде зареждана с мощност от 100 кВт, издържайки голям брой цикли на зареждане. Някои от конкурентите на C3 не предлагат дори възможност за зареждане с постоянен ток. По-малката батерия с 30 кВтч може да се зарежда от DC система с мощност 30 кВт, и при двата варианта са възможни зареждания с трифазен (11 кВт) и монофазен ток (1,8 кВт, 3,7 кВт и 7,4 кВт). Това се дължи както на качествата на клетките, така и на ефективната система за охлаждане, интегрирана в здравата алуминиева сандвичева конструкция с размери 1537 х 1137 х 258 мм. Теглото и е около 350 кг, но общото тегло е с 256 кг по-високо от това на версията с ДВГ.
Захранването и задвижването са базирани на по-популярната и по-достъпна 400 волтова архитектура и включва задвижващия предния мост електрически мотор с постоянни магнити, Това решение при електрическите мотори има най-висока ефективност в широк оборотен диапазон заради липсата на необходимост от електричество за създаване на магнитно поле в ротора. Самият електрическият мотор се произвежда от съвместното предприятие на Stellantis и Nidec eMotors и задвижва предния мост с помощта на едностепенна предавателна кутия с общо предавателно число от 15,05:1 (главно предаване 4,12:1 и едностепенна трансмисия 3,653:1). В зависимост от размера на батерията (30 кВтч или 44 кВтч) максималната мощност на двигателя (кратковременно при заряд на батерията над определено ниво) е 60 (81 к.с.) или 83 кВт (113 к.с.) и постоянна около 55 кВт и в двата случая. Сравнително късото общо предавателно число е основа за това високооборотният мотор с въртящ момент от 124 Нм (в диапазона 0-5250 об./мин) да осигури оптималната динамика на ускорение и максимална скорост, отчитайки факта че максималната му мощност се запазва в диапазона от 6500 до 9030 об./мин. Последното се дължи на факта че кривата на снижаване на въртящия момент се компенсира от тази на увеличаването на оборотите. Така, при движение с максималната скорост от около 130 км/ч се достигат и максималните оборотни режими на електрическата машина. Управляващата силова електроника и отоплителната система са разположени над електромотора и дават възможност за намаляване на дължината на силовите кабели.
Производственият процес е ключов за изграждането на въпросната платформа и създаване на автомобил, както с високо ниво на безопасност, така и с цялостно усещане за качество и здравина. Това става във високотехнологичния завод на Stellantis в Търнава, Словакия, който е с изключителна степен на автоматизация на поточните линии. То включва цехове за пресоване, заваряване, сглобяване на автомобила, качествен контрол и сглобяване на акумулаторни батерии. Резултатът от това е каросерия с равномерни и малки фуги, създаваща усещане за цялостност и завършеност на дизайна с неговите характерни скулптурирани форми и насоченост към SUV сегмента.
Текст: Георги Колев
Кликнете на изображението и се запознайте с конкретни ценови предложения за модела